Pipework Support Surveys Overview
Pipework support surveys, also known as hanger surveys, are visual inspections of nuclear power plant pipework and its supports, which are undertaken during operation and shut down modes. The results are used to confirm that pipe supports are operating as intended and are not degraded, damaged, seized or at the end of their travel range.
Regular inspections of pipework supports help to maintain long-term power plant integrity by helping to ensure that additional stresses are not encountered. Assessments of pipework systems and analysis of data gathered during inspections, including comparisons with historical records, ensures that issues can be identified and remediated, guaranteeing the piping systems will continue to function safely and efficiently.
Our longstanding relationship with both UK AGR (Advanced Gas Reactor) and PWR (Pressurized Water Reactor) plant operators has equipped us with valuable expertise regarding inspection and maintenance of pipework systems. This wealth of knowledge enables us to offer high-quality pipework support surveys across a diverse range of industries including civil nuclear, power generation, defense, chemical, oil and gas.
Our pipework support surveys provide clients with clear maintenance recommendations that ensure power plant safety and reliability. This helps to prevent downtime, minimize safety incidents, reduce maintenance costs, and improve operational efficiency — ultimately supporting effective asset management and reducing unplanned and potentially dangerous events.
Why Our Pipework Support Surveys?
-
Custom Tailored Solutions
The results of our pipe support surveys can help you identify potential defects which have gone unnoticed. This can include gagged supports, potential mechanism blockages, broken or distorted components, and interference with adjacent supports and equipment.
-
Continued Support
We review survey observations in combination with historical movements, design movements, and theoretical movements from pipework models. Afterwards, our team provides clear advice on maintenance recommendations to ensure continued safety and reliability of the plant.
-
International Experience
Our team has experience conducting pipe support surveys in various types of power plants, from advanced gas-cooled power plants in the UK to CANDU plants in North America and Europe.
-
Full Plant Walkdowns
We conduct plant walkdowns and physically inspect the condition of the pipe support systems, examine recent pipe travel positions, and review load path components.
Pipework Support Survey Technical Abilities
The Importance of Pipework Inspections
Our operational experience (OPEX) shows that poorly maintained or imbalanced pipework systems can lead to significant issues. Regular pipe support surveys are a proven and effective way to identify early signs of failure and minimize associated risks. There are several reasons why these surveys are so important:
- There is a significant industrial safety risk due to the stored energy in sprung pipe supports.
- The commercial impact of pipework failure on the secondary systems can also be significant.
- There are age-related degradation mechanisms for sprung pipe supports. Therefore, the incidence of hanger failures or issues will increase with plant age.
- Failures are contributed to by supports not functioning as designed (due to misalignments, wear, or components becoming bent).
- Supports are engineered to provide specific restraint to pipework, this can be upwards force for sprung supports, but also applies to gaps on limit stops and guides. If gaps are incorrectly set, or not present when they should be, this can damage the pipework.
- Easily detectable issues with pipework hangers such as being out of range (‘topped’ or ‘bottomed’) can lead to pipework failure. High energy pipework failures have severe industrial safety and commercial consequences.
- Dynamic behaviour of the pipework has implications on the structural integrity of its supports (vibration, swaying or transient events).
- Failure of a single pipe support in operation has implications on adjacent pipe supports and components which would take on extra load.
- Maintenance induced adverse conditions can be introduced inadvertently (staff may damage pipe supports, clashes of support components/pipework with scaffolding, or non-removal of temporary pipework fixings/restraints).
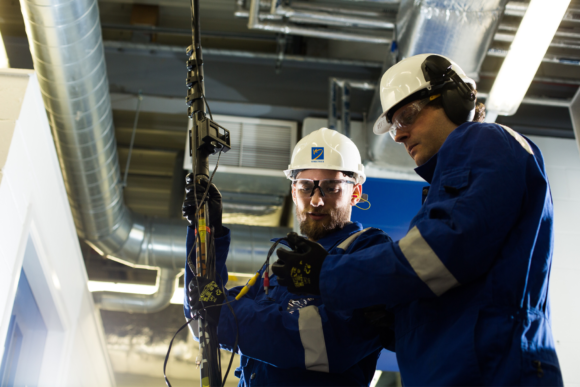
Pipework Support Inspection
Our team conducts thorough plant walkdowns to visually inspect the condition of all pipework and pipe supports, meticulously documenting the condition and travel position of constant, variable and rigid types of supports. We assess all load path components and consider potential defects/issues such as:
- End of travel reached – topped/bottomed
- Gagged/restricted supports
- Potential mechanism blockage due to debris
- Broken or distorted components
- Components in poor condition
- Loose or missing nuts, bolts or locknuts
- Misalignment
- Interference/clashing with adjacent pipelines, supports, steelwork or equipment
- Corrosion
- Vibration
- Slumping of pipelines
All observations are noted as part of the survey so that they can be considered against knowledge of plant operations and maintenance procedures to inform recommendations for remedial work.
Pipework supports on high temperature pipework systems may be of particular interest since supports functioning as per their design intent allows for thermal expansion of the pipework without excessively large stresses within the pipework developing. For high temperature systems, survey travel scale position results are used to build a database of movements. This database is reviewed against design movements and any historical data available so our experts can ensure the pipework is operating within design intent and can assess the implications of any observed issues.
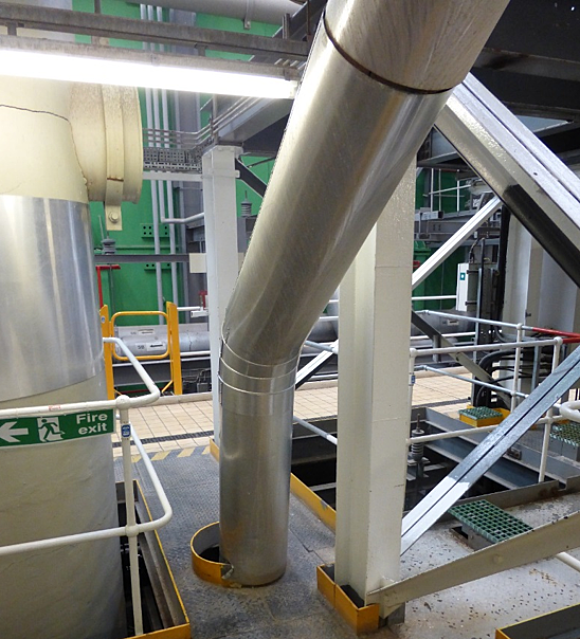
Pipework Support Survey Methodology
Our method is grounded in a systematic approach to both inspections and ongoing pipeline monitoring, tailored to the systems in scope, helping to ensure the correct level of inspection is undertaken to maintain pipework integrity. Key stages include:
1. Scoping and Planning: Identify systems that would benefit from pipework support surveys by undertaking research to understand operating conditions and pipework supports in use, identifying suitable inspection intervals to satisfy safety requirements, and compiling the information required (system drawings, support details, etc) to undertake inspections.
2. Plant Surveys: Undertake full surveys of pipework supports in its various operating conditions to determine the condition and movement of the systems.
3. Audit: Undertaken after every plant survey to ensure a high level of quality is maintained. The survey results are subject to an independent audit, which will look at any issues raised in the surveys and a random sampling of the survey results to ensure that the appropriate remedial actions are undertaken.
4. Data Comparison and Trend Monitoring: A database of each surveyed system is created and used to compare the condition and movement of the system over time, comparing initial records against design conditions or calculated theoretical movements and then over time against the historical survey results. This allows long-term pipeline monitoring helping to detect issues early, in turn allowing proactive solutions which prevent failure from occurring.
5. Reporting: A full written report is provided after each survey and audit reviewing the condition of the pipework and deviations from previous surveys. Each report will provide recommendations for remedial work and the effect of completed remedial work, while also acting as a record for any outstanding actions.
6. Remediation Support: Our experts can provide support to the remediation process to ensure the best possible outcome.
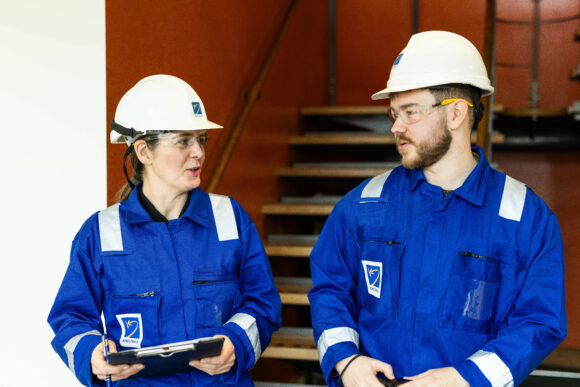
Our Proven Experience
Quality Assurance & Technical Standards
- ISO 9001
- Quality Management System