Project Overview
The Bruce Reactor Inspection and Maintenance System (BRIMS) is a system of tooling and processes that delivers the full suite of fuel channel inspection and maintenance (FCIM) equipment at Bruce A and B in an efficient and fully integrated manner, using a common delivery platform.
BRIMS operates on the reactor face once mounted on the Reactor Area Bridge (RAB) that is to deliver any of the available specialized FCIM programs; BRIMS-ANDE, CWEST*, SLAR, MODAR and Replica.
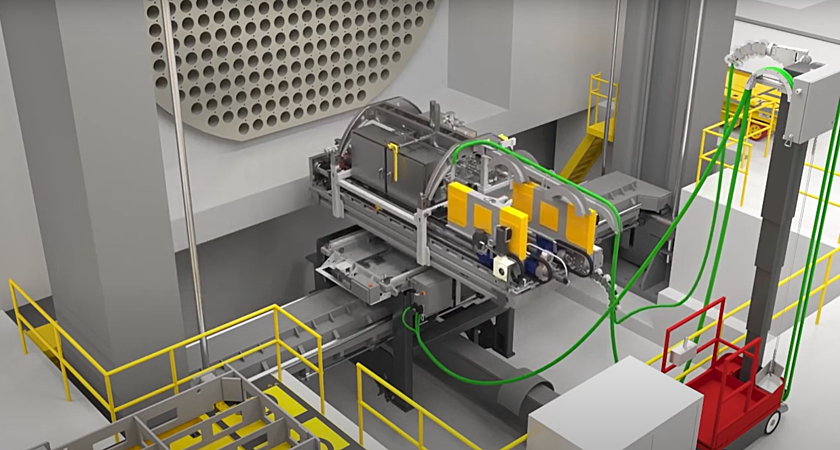
The maintenance and execution program was a series of projects with the following objectives:
- Free Bruce Power resources to concentrate on operating unit maintenance
- Reduce overall outage preparation and maintenance costs by reducing the number of people required to plan, prepare, perform and report maintenance and test activities and consolidating the management of spares within a single entity
- Establish the ability to maintain and test equipment in parallel with outages (instead of between) in order to provide time for correct maintenance, testing and improvements
- Entrench the best WANO maintenance practices (as outlined in Bruce Power’s Maintenance and Testing Programs) in one facility so that work is performed in a systematic, methodical and documented manner which should result in improved reliability and production efficiency of the BRIMS system in an outage. While the Bruce Power Programs do not have to be followed verbatim, the desire is that the intent of them be followed and that Bruce Power’s Enterprise Asset Management system (PassPort or Maximo) be the repository for the most up to date configuration and procedural information
- Establish a dedicated resource pool on an ongoing basis ready to supplement outage execution crews in the event of a major unplanned maintenance activity
As a result of the above, the maintenance of BRIMS 1 and BRIMS 2 (the two BRIMS tools) will be done at the KI-North facility in preparation for execution during planned outages at Bruce Power.
Our Experience
The specific fuel channel tool head programs BRIMS delivers, on-reactor during the planned outages include ANDE, CWEST*, Replica, SLAR and/or MODAR. We will be responsible for the following:
- Pre/post-maintenance activities on the BRIMS delivery machine and Channel Access Device (ChAD)
- Complete the lead-in scope of work and crew support of in-vault activities for all tool programs
- Support the decontamination of all vault equipment
- Support the transportation of equipment in the station, across site and off site to a maintenance facility
- Support the installation of Vendor support equipment (in vault)
- Maintain a highly motivated work force to complete the above objectives
- Maintain improving standards for training
How We Helped
To most effectively help Bruce Power achieve tehir objectives we developed a facility for the maintenance of BRIMS 1 and BRIMS 2 (the two BRIMS tools) at or KI-North close ot the Bruce Power site.
The specific fuel channel tool head programs BRIMS delivers, on-reactor during the planned outages include ANDE, CWEST*, Replica, SLAR and/or MODAR and we are responsible for the following:
- Pre/post-maintenance activities on the BRIMS delivery machine and Channel Access Device (ChAD)
- Complete the lead-in scope of work and crew support of in-vault activities for all tool programs
- Support the decontamination of all vault equipment
- Support the transportation of equipment in the station, across site and off site to a maintenance facility
- Support the installation of Vendor support equipment (in vault)
- Maintain a highly motivated work force to complete the above objectives
- Maintain improving standards for training
We developed innovation strategies and collaborated with client to improve procedures and reports. showcasing our understanding of project interrelationships and interdependencies, working with multidisciplinary teams, and identifying gaps in and improving current procedures.
Some of the Technical and Commercial Challenges Faced were:
1. Implementation/Establishing of Project Controls Processes with Client’s Staff.
Mitigation - Several tactics were employed to address this challenge:
- Support from clients Executive/Senior management is key. Change management emails/direction should come from them
- Simplified and automated processes get more buy in than manual work. Automate and think how the users will feel if we add more work
2. Access to Client Data, Process and Integration as a Team
Mitigation – Several tactics were employed to address this challenge:
- Create and provide Conflict of Interest training to staff support client. Ensure client interest is paramount
- Prove to client there is established Ring Fence training for all staff
- Simplified and automated process to review and approve procedures and other deliverables
3. Changing Client Requirements
Mitigation – Several tactics were employed to address this challenge:
- Make processes adaptable and nimble as requirements change based on multiple factors
- Be prepared to go back to drawing board to start over while utilizing the strength of what was planned before
4. Integration of Schedules
Mitigation – Several tactics were employed to address this challenge:
- Make processes adaptable and nimble as requirements change based on multiple factors
- Always be ready to accommodate critical path activities and changes
*CWEST not available for sale outside of Canada until after November 30, 2027.