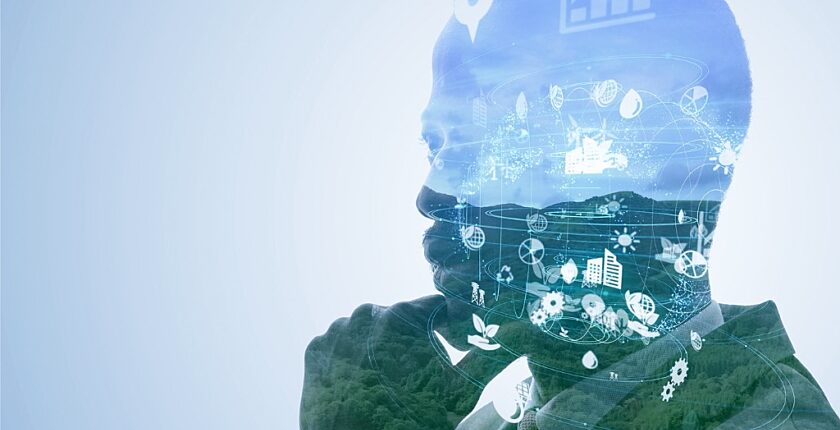
We are sustainably powering a clean energy future for today and tomorrow.
Our industry leading subject matter experts, state-of-the art facilities and innovative solutions are more than just individual offerings, they are the culmination of decades of experience providing comprehensive lifecycle management and programmatic services across the power generation, transmission and distribution ecosystems.
We are here to resolve your toughest challenges.