Project Overview
The Extended West Shift Plus (EWSP) Stop Collar (SC) assembly configuration for Bruce Power had to be tested to help demonstrate that the design would retain structural integrity over its remaining service life.
How We Helped
A Stop Collar Test Facility (SCTF) was constructed to allow a full-size simulated SC assembly to be loaded in axial, bending, lateral, and torsion modalities. These loads were applied to the SC assembly through a full-size End Fitting (EF) with an End Fitting Attachment (EFA) ring. The loads were transferred through the EWSP SC welds via the EFA ring and into the simulated SC. The EWSP welds were fabricated using suitably representative welding equipment and procedures to those intended for the execution of the field welds in the reactor.
Loads were applied through a series of actuators uniaxially, as was done in the design analysis. Strain was then measured on the stop collar through high temperature strain gauges and captured using a Digital Image Correlation (DIC) system. The facility was then used to load the stop collar to Level B service limits for comparison to design analysis and to 3x Level B service limits to attempt to discern a collapse load.
We designed, built, and executed the test program to support the design analysis of the stop collar and stop collar welds. The results of the test program, together with the design analysis, demonstrated that the new stop collar design would not experience plastic collapse or a fatigue failure during its planned service life. These inputs were used as part of the client’s regulatory submission to support justification of the life extension of the unit.
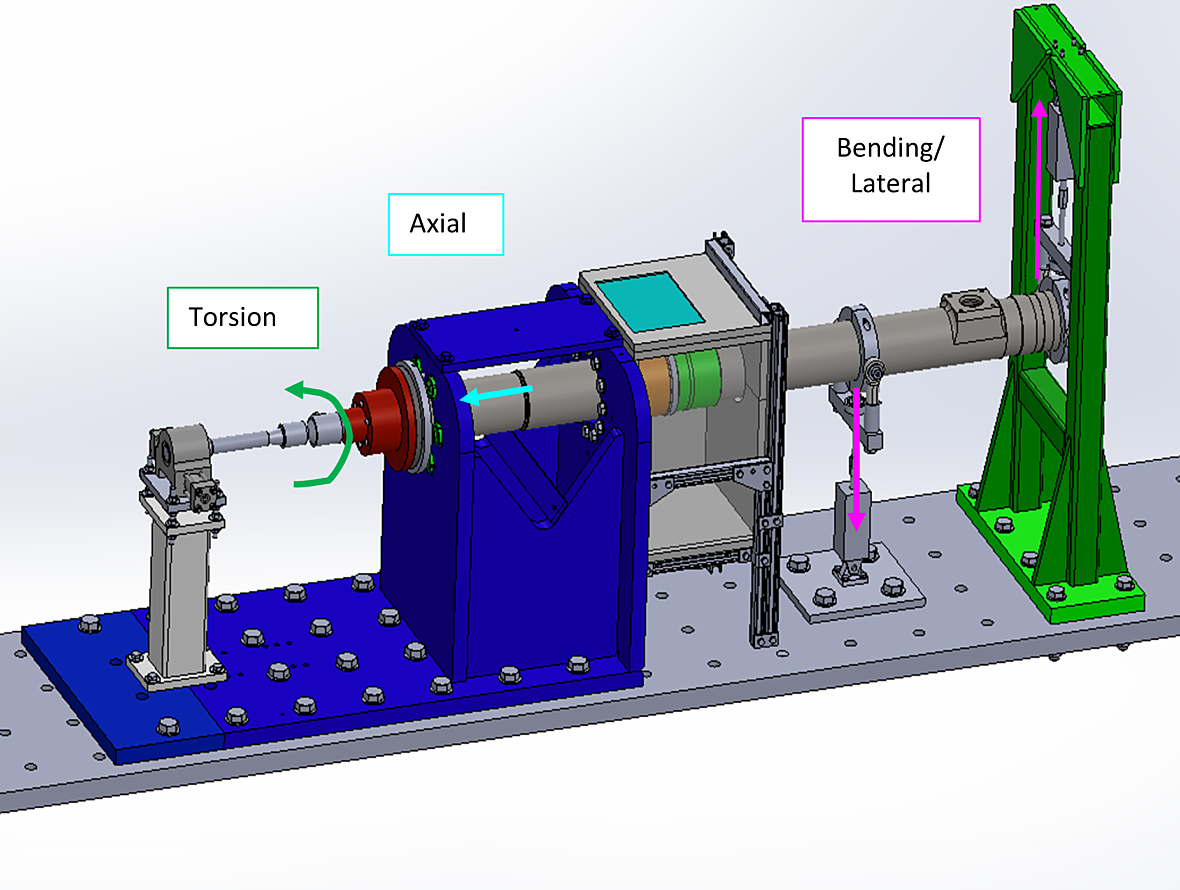